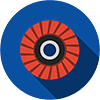
Abrasives
Abrasives are materials, often in powder or grain form, that have the ability to wear, polish or smooth other surfaces through friction. The types of abrasives for machine shops vary widely and include abrasive paper, abrasive discs, grinding wheels and abrasive pastes. The choice of abrasive type depends on the specific application and the type of material to be processed.
The use of abrasives in machining is vast and diverse. They are used to cut, grind, polish and remove excess material from metal surfaces. For example, during the finishing phase, abrasives help to achieve a smooth and polished surface, thus improving the aesthetic appearance and functionality of the workpiece.
The advantages of industrial abrasives are numerous. First of all, they improve the precision and quality of the work, allowing for perfectly smooth and imperfection-free surfaces. Furthermore, abrasives reduce machining time, increasing production efficiency. Industrial abrasives are also crucial for safety, as they reduce the risk of defects in mechanical components that could cause malfunctions.
Choosing the right abrasives for the metal is crucial for optimal results. It is important to consider the hardness of the material to be machined, the grit size of the abrasive and the type of machining required. For example, for very hard materials such as stainless steel, it is advisable to use abrasives with a fine grit and high hardness. Furthermore, the shape of the abrasive, such as discs or belts, must be chosen according to the machine tool being used.
Advanced techniques for using abrasives include the use of specific machines, such as angle grinders and belt sanders, which improve the precision and efficiency of the machining process. In addition, the application of lubricants and coolants when using abrasives can prolong the life of the abrasive and improve the quality of the finish.
Frequently Asked Questions about Abrasives
What are the main types of abrasives used in machine shops?
The main types of abrasives include abrasive paper, abrasive discs, grinding wheels and abrasive pastes, each with specific applications depending on the type of work and material.
How can I improve the life of abrasives?
To improve the life of abrasives, it is essential to use appropriate lubricants and coolants, keep tools clean and choose the right type of abrasive for each specific application.
In conclusion, abrasives are indispensable tools in machine shops, offering a wide range of applications that improve the efficiency and quality of work. With the right knowledge and proper use, it is possible to make the most of the advantages offered by abrasives, ensuring optimal and lasting results.
-
Cutting discs8 products
-
Deburring grinding wheel5 products
-
Flap discs17 products
-
Fabric discs for surface treatment5 products
-
Abrasive fibre discs with Velcro28 products
-
Abrasive cloth in rolls, sheets and bands21 products
-
Flap wheels with pin and abrasive wheel with hole5 products
-
Abrasive wheels for buffing machines3 products
-
Abrasive spiral bands7 products
-
Abrasive brushes19 products
-
Flexible sanders1 products
-
Mounted grinding discs9 products
-
Polishing felt15 products
-
Solid carbide rotary cutters20 products
-
HSS rotary cutters6 products
-
Abrasive wheels for sharpening and grinding12 products
-
Diamond needle files7 products
-
Grinding stone6 products
-
Diamond paste4 products
-
Abrasive stones16 products
-
Files and rasps22 products
-
Diamond files4 products
-
Grinders and polishing equipment11 products