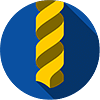
Solid cutting tools
In the world of machine shops, the importance of integral cutting tools is undeniable. These tools, essential for metalworking, offer precision, durability and high performance.
Integral cutting tools are precision tools made entirely from a single piece of material, usually high-speed steel (HSS) or tungsten carbide. These tools are designed for cutting, drilling, milling and turning operations in high-precision environments, such as machine shops. Their monolithic structure ensures greater strength and stability during use.
Integral cutting tools find application in a wide range of machining operations. They are ideal for:
- Milling: Used to create flat surfaces, grooves and other complex shapes on metal parts.
- Drilling: Essential for creating precise holes in metal materials.
Turning: Used for cylindrical, tapering or threading operations on lathes.
The correct use of these tools requires a thorough knowledge of cutting speeds, angles of attack and cooling techniques. Their maintenance is crucial to ensure optimum performance and longevity.
Integral cutting tools offer numerous advantages that make them indispensable in machine shops:
- High precision: The monolithic structure allows very tight tolerances to be maintained, which is essential for precision machining.
- Durability: High-quality materials such as HSS and tungsten carbide ensure a long service life even under extreme working conditions.
- Efficiency: Reduced machine downtime due to increased reliability and wear resistance.
- Versatility: Suitable for various operations, reducing the need for frequent tool changes.
Answers to Frequently Asked Questions
What are the best integral cutting tools for precision mechanics?
The choice of the best tools depends on the type of machining and the material to be machined. However, tungsten carbide tools are often preferred for their superior hardness and strength.
How do you maintain integral cutting tools?
Maintenance includes regular cleaning, periodic sharpening and checking for wear. It is also important to use cooling fluids correctly to avoid overheating.
What are the main factors to consider when choosing integral cutting tools?
The main factors include the tool material, the type of machining, the cutting speed and the technical specifications required by the project.
In conclusion, integral cutting tools are essential for any machine shop aiming for precision, efficiency and durability. Investing in high quality tools and their proper maintenance not only improves operational performance, but also guarantees a significant return in terms of productivity and quality of work performed.
-
Solid carbide drills31 products
-
HSS drills46 products
-
Taps for threading98 products
-
Thread milling cutters4 products
-
Solid carbide end mills84 products
-
HSS and high speed steel end mills20 products
-
Reamers for metal11 products
-
Countersinks16 products
-
Counterbores6 products
-
Band saw blades14 products
-
Circular saw blades6 products