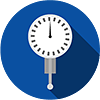
Measuring and precision tools
In a machine shop, precision is paramount. Every component, every part must be measured accurately to ensure that it fits perfectly and functions as intended. Measuring and precision instruments are therefore essential for day-to-day work. These tools not only ensure that dimensions are correct, but also help to improve the efficiency and quality of work.
Measuring and precision tools are devices used to determine the physical dimensions of objects. These include micrometers, calipers, dial gauges and optical measuring instruments. Each instrument is designed to offer a specific level of precision and accuracy, making them indispensable in machine shops where error tolerance is minimal.
In a mechanical environment, these instruments are used for a variety of purposes:
- Quality control: They check that the parts produced comply with technical specifications.
- Assembly: They ensure that parts assemble correctly without defects.
- Maintenance: They measure the wear of components to decide when to replace them.
The correct use of measuring instruments is crucial for reliable results:
- Calibration: Ensure that instruments are calibrated regularly to maintain their accuracy.
- Conditions of use: Use them in controlled environments to avoid variations in temperature and humidity that can affect measurements.
- Cleaning: Keep instruments clean and free of debris to avoid incorrect readings.
Measuring and precision instruments offer many benefits, including:
- Accuracy: They provide precise measurements that reduce production errors.
- Efficiency: They improve the speed of operations by reducing the time needed to check component dimensions.
- Quality: They help maintain high quality standards, essential for customer satisfaction and company reputation.
Answers to Frequently Asked Questions
1. What are the most common measuring instruments in a machine shop?
The most common are slide gauges, micrometers, dial gauges and depth gauges.
2. How is the calibration of measuring instruments carried out?
Calibration is carried out using gauge blocks or other reference instruments traceable to international standards.
3. How often should instruments be calibrated?
It depends on usage, but quarterly calibration is generally recommended.
4. Are digital measuring instruments better than analogue ones?
Both have their advantages: digital ones offer quick and easy readings, while analogue ones can be more robust and do not require batteries.
Measuring and precision instruments are the beating heart of machine shops, ensuring that every component produced is up to the required standard. Investing in high quality instruments and maintaining a strict calibration and maintenance routine improves accuracy, efficiency and overall quality of work.
-
Digital calipers with readings to 0.0130 products
-
Analogue calipers17 products
-
Digital micrometers15 products
-
Analogue micrometers19 products
-
Bore gauges9 products
-
Snap gauges8 products
-
Digital gauges21 products
-
Analogue gauges12 products
-
Touch probes12 products
-
Zero setters and edge finders6 products
-
Inspection plates6 products
-
Altimeters7 products
-
Height gauges7 products
-
Squares and levels19 products
-
Threaded rings17 products
-
Gauge blocks4 products
-
Calibrated tapes and thickness gauges14 products
-
Digital and analogue hardness testers10 products
-
Roughness testers8 products
-
Microscopes, lenses and visors23 products
-
Video endoscopes0 products
-
Digital thermo-hygrometer to measure moisture9 products
-
Reset benches2 products
-
Optical profile projector2 products
-
Professional, digital dynamometers4 products
-
Laboratory scales8 products
-
Digital amperometric pliers2 products
-
Thickness and adhesion gauges26 products