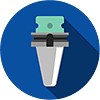
Clamping systems
At the heart of machine shops, precision and safety are crucial elements to ensure effective and reliable operations. Clamping systems play a key role in this context, offering indispensable solutions for clamping and stabilising components during complex machining operations.
Clamping systems are devices used to clamp, fix or hold parts during machining. They can be manual, pneumatic or hydraulic, each with specific characteristics that make them suitable for different applications. These systems ensure that parts remain stationary, reducing the risk of errors and improving machining accuracy.
Types of Clamping Systems
- Manual Clamping Systems
Manual clamping systems are among the simplest and most versatile. Used for operations requiring precision and direct control, these devices are ideal for small-scale work or applications where fine adjustment is essential.
- Hydraulic Clamping Systems
Hydraulic clamping systems utilise fluid pressure to exert a high and constant force. These systems are ideal for applications requiring strong and uniform clamping, such as the machining of hard materials or large components.
- Pneumatic Clamping Systems
Pneumatic clamping systems use compressed air to apply force. They are particularly useful in applications requiring speed and repeatability, as they can be automated and precisely controlled.
Advantages of Clamping Systems
- Accuracy and Reliability
The use of proper clamping systems ensures that components remain stationary during machining, improving the accuracy of cuts and holes. This reduces errors and increases the overall quality of the final product.
- Safety at Work
Clamping systems improve safety on the shop floor by preventing sudden movement of parts and reducing the risk of accidents. Manual, hydraulic and pneumatic devices are designed to provide safe clamping, protecting both workers and equipment.
- Operational Efficiency
Thanks to their ability to hold parts in place without the need for constant adjustment, clamping systems increase the efficiency of operations. This translates into reduced processing times and increased productivity.
In machine shops, clamping systems are used at various stages of the production process. From precision work on small components to large industrial assemblies, these devices ensure that every part is handled with the utmost care and accuracy.
Manual clamping systems are often used in craft or high-precision work, where direct control is crucial. Hydraulic systems, with their strength and stability, are ideal for machining robust materials. Finally, pneumatic systems, with their speed and automation, are perfect for mass production lines.
Frequently Asked Questions
What is the difference between hydraulic and pneumatic clamping systems?
Hydraulic systems use fluids to apply a constant, powerful force, while pneumatic systems use compressed air, offering speed and ease of automation.
What are the advantages of manual clamping systems?
Manual systems offer precise and direct control, ideal for jobs requiring fine adjustments and precision on a small scale.
Clamping systems are essential tools in machine shops, providing precision, safety and operational efficiency. Whether manual, hydraulic or pneumatic, their adoption can transform the way work is performed, leading to high quality results and a safer working environment.
-
Spindles SK DIN 6987129 products
-
Chucks MAS 403 BT27 products
-
Chucks HSK-A DIN 69893A21 products
-
Chucks DIN 2080 and cylindrical14 products
-
Spring collects for locking and chucks74 products
-
Angle heads4 products
-
Driven tool holders30 products
-
Self centering chucks20 products
-
Magnetic plates5 products
-
Clamping Jaws. Live centers, face drivers17 products
-
Various accessories for clamping20 products
-
Zero-point clamping systems43 products